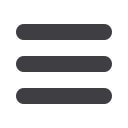
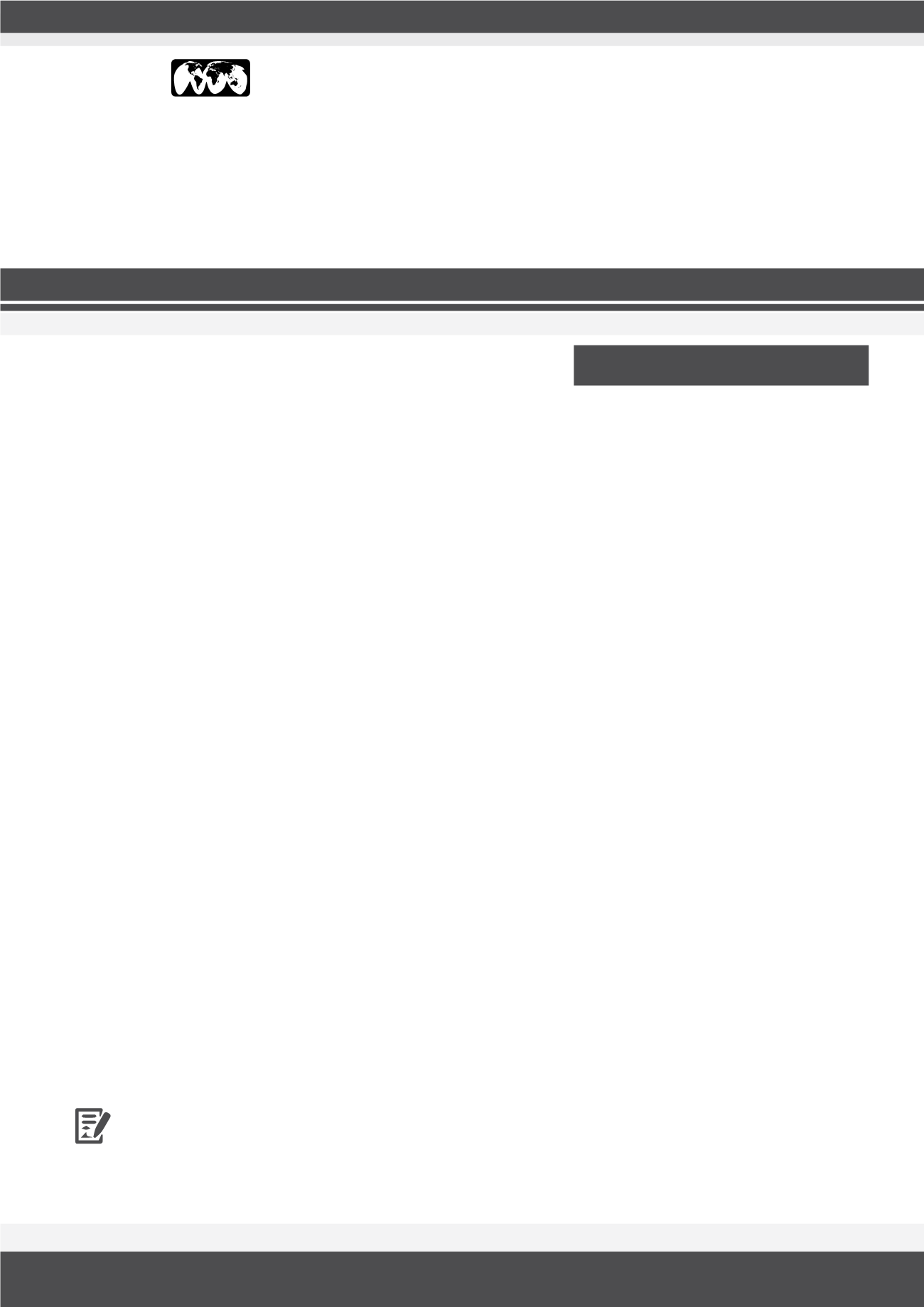
Page 42
Note:
Biotechnology Congress 2018 & Emerging Materials 2018
Biomedical Research
|
ISSN: 0976-1683
|
Volume 29
S e p t e m b e r 0 6 - 0 7 , 2 0 1 8 | B a n g k o k , T h a i l a n d
allied
academies
Joint Event on
EMERGING MATERIALS AND NANOTECHNOLOGY
BIOTECHNOLOGY
&
Annual Congress on
Global Congress on
Samia Danuta Brejão de Souza et al., Biomed Res 2018, Volume 29 | DOI: 10.4066/biomedicalresearch-C4-011
CHARACTERIZATION BY ENF OF SAMPLES
WELDED BY ELECTRIC RESISTANCE
WELDING PROCESS AND CONDITIONED IN
UV RADIATION CHAMBER
Samia Danuta Brejão de Souza, Edson Cocchieri Botelho
and
Luís
Rogerio de Oliveira Hein
São Paulo State University, Brazil
O
ne of the limitations of the use of composites is to obtain parts without
the presence of joints or joints between their components, which they are
necessary due to inherent limitations in themanufacturing process. The union
of pieces with thermoplastic composites can be a critical factor, because
depending on the type of union used, they can generate concentration
points and be susceptible to fracture (COSTA, 2011). Resistance welding
is a specific technique for joining thermoplastic composites. The process
uses the property of flow of the thermoplastic matrix when heated above
the melting temperature (semi-crystalline polymers). It can be characterized
as the union of parts through the fusion and consolidation under pressure.
The ENF (end notched flexure) test was done to obtain the value of fracture
toughnessGIIc. The PEEK/CF samples had the highest value (1114.8±157.2 J/
mm) in relation to the welded sample (679.6±346.0 J/mm) and to the welded
sample conditioned in the UV chamber (724.4±421.4 J/mm). This behavior
can be attributed to the non-existence of the metal mesh at the welding
interface, which acts as a cracking propagation concentrator. With the results
of ENF, it can be concluded that the shearing stress average is close to the
yield strength average for PEEK pressed samples (801.5±58.6/795.9±57.6
MPa), PEEK welded (341.9±55.9/314.6±50.7 MPa) and PEEK welded and
conditioned in the UV chamber (449.5±111.9/414.9±115.7 MPa). However,
the fracture toughness mode is relatively low, when compared to the available
values in the literature for other composites involving thermoplastic matrices
and carbon fibers.
Samia Danuta Brejão de Souza did her Bachelor of
Science in Materials Engineering from UNESP– Uni-
versidade Estadual Paulista in São Paulo, Brazil. Her
graduate thesis was addressed the ceramic mate-
rials field, for prosthesis parts as well as filters. Fur-
thermore, she has worked abroad at Institut für Ver-
bundwerkstoffe (Germany) as a guest Scientist on
induction welding process for PEEK/CF laminates to
compare these samples with results from specimens
manufactured through electrical resistance welding.
At present, she is pursuing her Pos-doc in UFRGS
(Federal University of Rio Grande do Sul – Brazil). The
project is about composites for ballistic armor.
samiadanuta@hotmail.comBIOGRAPHY