
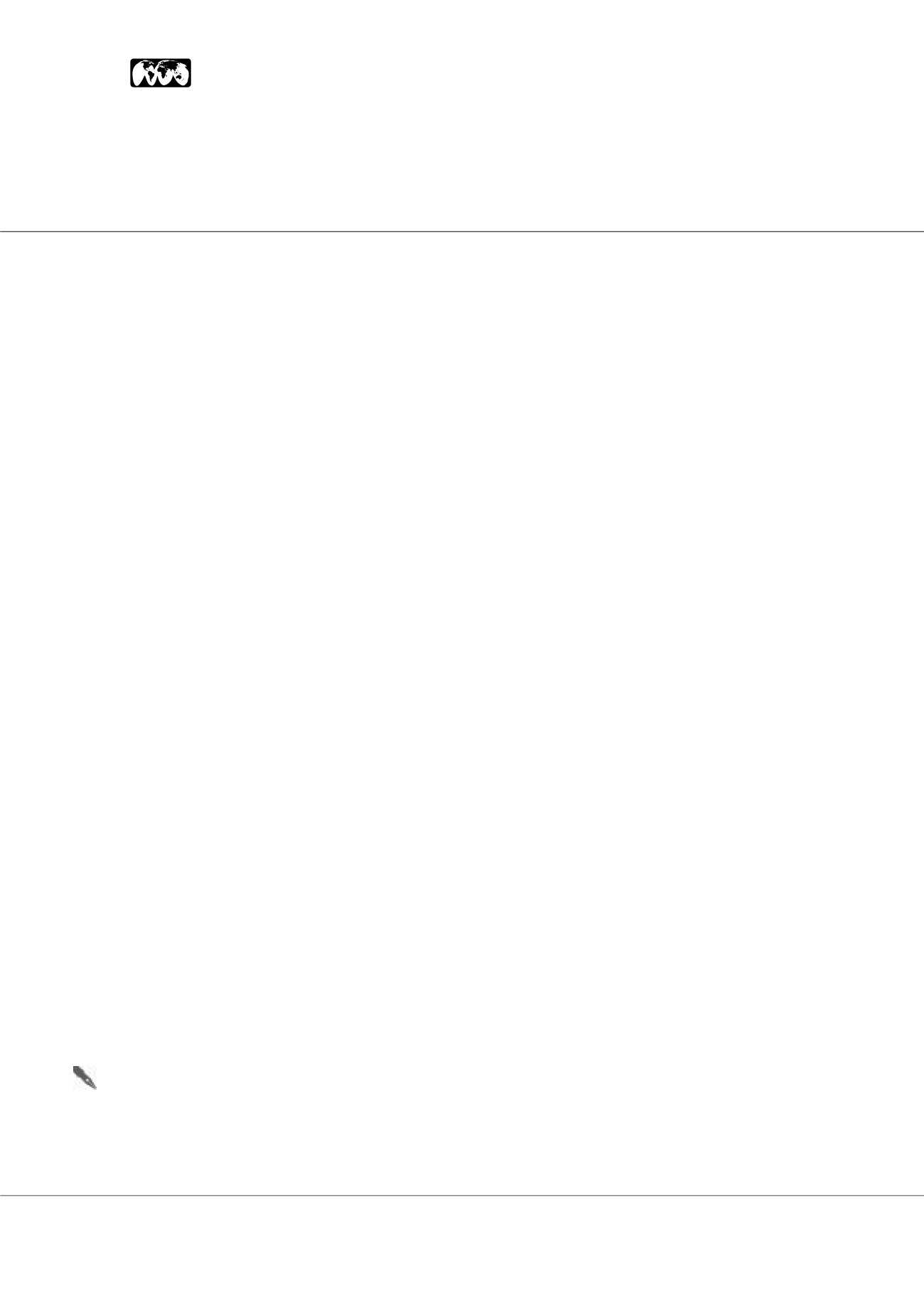
Page 41
allied
academies
Journal of Environmental Waste Management and Recycling | Volume 1
March 05-06, 2018 | London, UK
Recycling & Waste Management
5
th
International Conference on
Notes:
Total recycling of valuable metals from spent auto-catalyst
Jae-chun Lee, Ha B Trinh, Sookyung Kim
Korea University of Science and Technology, Korea
T
he cordierite (2MgO
.
2Al
2
O
3
.
5SiO
2
), the substrate of
auto-catalysts is generally coated with the thin layer of
γ
- Al
2
O
3
, which also contains the PGMs (Pt, Pd and Rh) as
active material and a mixture of additives (oxides of Ce, Zr,
La, Ni, Fe and alkaline-earth). The recycling of PGMs from
the spent auto-catalysts is becoming extremely attractive
as compared to the primary resources due to the higher
contents of PGMs, with several advantages such as simpler
process, lower cost, and lesser environmental pollution.
For decades the pyrometallurgical recycling processes
have been employed to extract PGMs from the spent auto-
catalyst. Though the pyrometallurgical processes are highly
efficient to recover PGMs, but they can’t recover other metal
components. In view of the depletion of primary resources
and climate changes associated with the gaseous emissions,
new strategies are required particularly to recycling all
valuable components. The hydrometallurgical routes may
offer such possibilities ensuring the recovery of almost all the
metals from the spent auto-catalyst, but require aggressive
acidic conditions and oxidants in high concentrations. In
order to develop an efficient and environmentally friendly
approach, we have investigated a new hydrometallurgical
process for the total recycling of other metal components
as well as PGMs from the spent auto-catalyst. The cordierite
substrate of the auto-catalysts was decomposed to dissolve
aluminum and magnesium using NaOH roasting and H
2
SO
4
leaching, leaving PGMs and cerium oxide in the residue.
PGMs were recovered to the extent of 99% by cementation
with Al whereas cerium oxide was recovered up to 90% by
hot digestion using H
2
SO
4
. The hydrometallurgical process
described in this study has a potential for sustainable
utilization of wastes to recycle all the metals.
Speaker Biography
Jae-chun Lee is currently Distinguished Principal Researcher in the Mineral Resources
Research Division at the Korea Institute of Geo science and Mineral Resources (KIGAM)
and a campus representative professor in the Department of Resources Recycling at
the Korea University of Science & Technology. Lee received his B.S. in metallurgical
engineering, M.S. and Ph.D. in Hydro metallurgy from Hanyang University, Korea. His
research deals with leaching, separation and purification of metals from primary and
secondary resources and material preparation by aqueous processing. His current
research focuses on the recycling of valuable metals from urban mine by hydro
metallurgical routes. He has authored over 200 articles. He is currently an Associate
Editor of Hydrometallurgy.
e:
jclee@kigam.re.kr