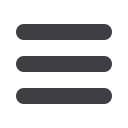
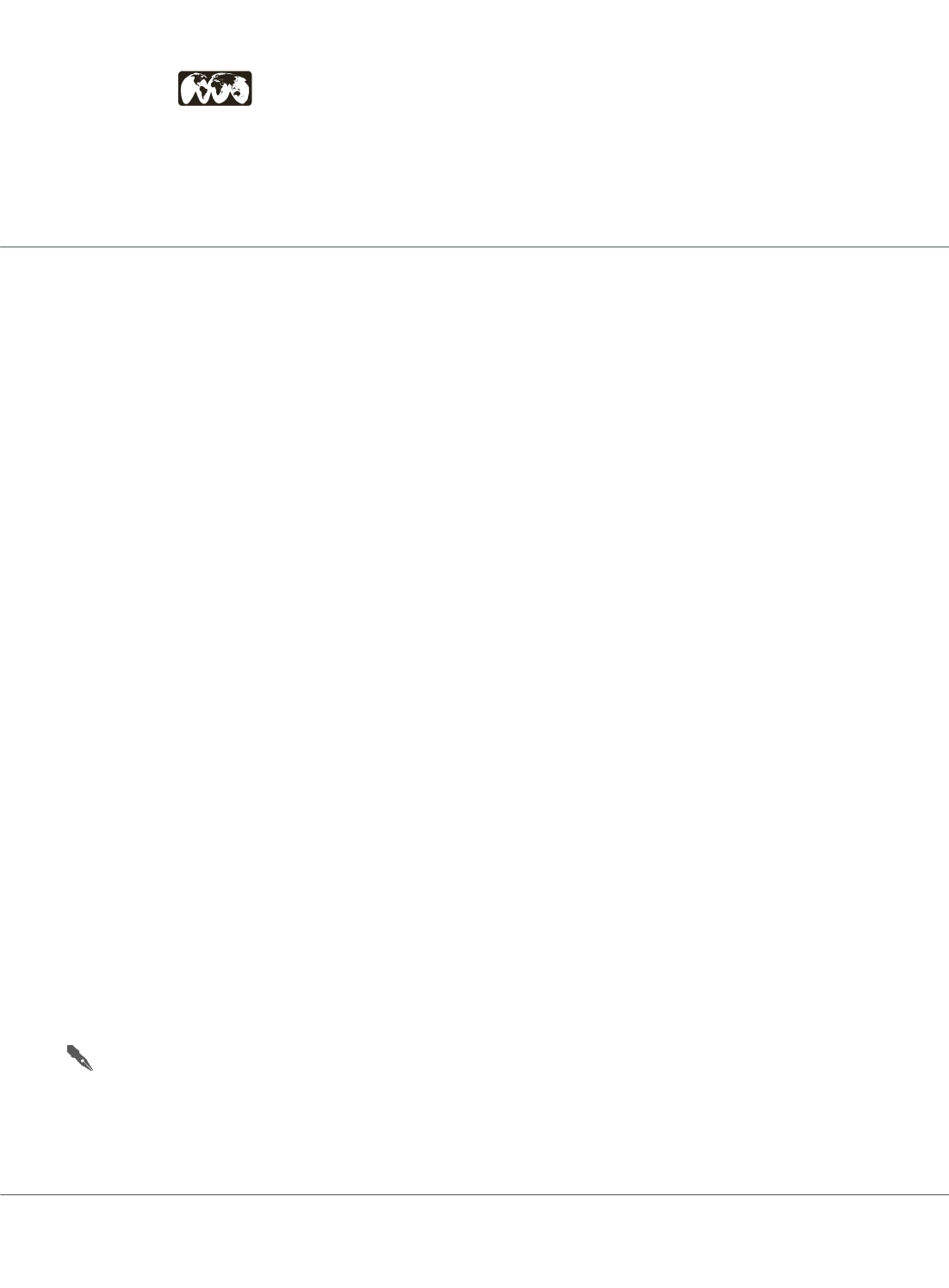
allied
academies
Page 49
Notes:
April 15-16, 2019 | Frankfurt, Germany
Applied Physics & Laser, Optics and Photonics
International Conference on
Materials Science and Nanotechnology | Volume: 3
Improving laser powder bed fusion additive manufacturing by X-ray tomography
Anton Du Plessis
1
, Igor Yadroitsev
2
and
Ina Yadroitsava
2
1
Stellenbosch University, South Africa
2
Central University of Technology, South Africa
L
aser powder bed fusion (LPBF) is a form of
additive manufacturing which allows detailed
and complex functional components to be
manufactured – recently in many new organic
and biomimetic designs. This technology has the
potential to disrupt the manufacturing industry
through its freedomof designandnewparadigmof
complexity in parts that can be produced. Despite
this potential, the processes need to be optimized
to achieve acceptable mechanical properties and
enhance the reliability of these types of parts.
Using X-ray tomography to inspect final parts is
one technique which has become almost routine
in this industry – the non-destructive nature and
the insights provided outweigh the costs involved.
What is not well known yet – is that the laser
powder bed fusion processes may be optimized
using the technique in many other ways than
simply inspecting the final part. The powder
feedstock can be analyzed for sphericity, lack of
porosity and lack of impurities. Small coupon
samples can be analyzed for micro porosity
distribution – this provides insight into defect
formation regimes and can assist in optimizing
the scan strategy, hatch spacing, contour
scanning parameters or the laser power or scan
speed, for example. Different regimes of process
inaccuracy lead to different types, shapes and
distributions of micro porosity, which is visualized
by X-ray tomography. Finally, these distributions
translate into the final complex parts which will
be demonstrated. Finally, small coupon samples
called witness specimens are built alongside
the complex part and are used as reference for
analysing the micro porosity and defects formed
during the process – for example for layered
stop-start flaws. Examples of all of these will be
discussed in the presentation, in the context of
improving and refining additive manufacturing
processes.
e
:
anton2@sun.ac.za