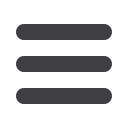
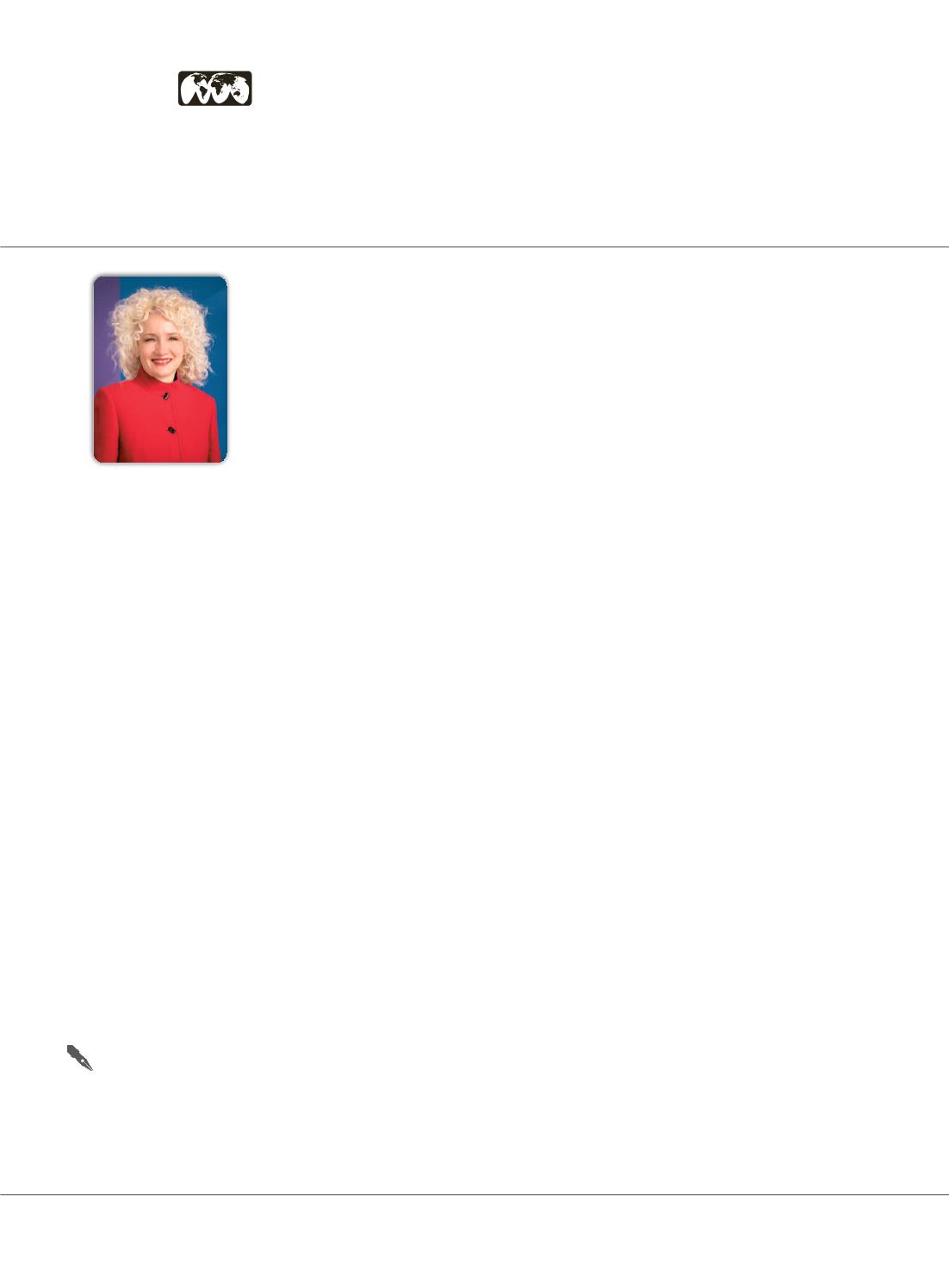
allied
academies
May 20-21, 2019 | Vienna, Austria
Biomaterials and Nanomaterials &
Materials Physics and Materials Science
2
nd
International Conference on
Page 16
Journal of Materials Science and Nanotechnology | Volume 3
F
uel cell electric vehicles (FCEVs) are demonstrating
commercial readiness: fully-functional fuel cell/
electric hybrid vehicles with >400 km range and refuel
times of <4 minutes have been shown to be feasible.
Leading automakers (including Toyota, Daimler, Ford,
Honda, Nissan, Hyundai, and GM) have supported,
and are continuing to support FCEV development and
deployment with billions of dollars of investment spent
to date and further significant investment planned. These
automakers foresee that FCEVs are a key option in the
overall advanced power-train portfolio that will allow
them to meet the complete range of customer needs
while at the same time complying with environmental,
energy efficiency, and regulatory requirements (especially
as zero emission vehicles, fuel economy, and greenhouse
gas policies are being developed). Some of the technical
barriers of polymer electrolyte membrane fuel cell
(PEMFC) technology have been clearly identified at a high
level. These involve materials cost, performance, reliability,
and durability. Currently, electrodes make up almost half
of the MEA cost and increases in catalyst efficiency and
manufacturing cost reduction in this area are expected to
have a large impact on the overall cost. The cost of catalyst
ink, even at large volume production of 500,000 units/year,
will still represent the highest cost component. However,
to be competitive with the internal combustion engine that
costs only $25-35/ kW for an entire engine, the cost of the
FC stack must be substantially reduced. In order to reduce
the cost, we designed low Pt loading catalyst, total loading
of 0.15 mg/cm
2
, and evaluated the stability and durability
of the low Pt loaded nano catalyst. In order to achieve the
highest performance and stability with a low Pt loading
catalyst, we optimized a gradient structure of the catalyst
with optimized, Pt, ionomer and carbon loading.
Speaker Biography
Radenka Maric is the vice president for research at the University of
Connecticut. She has been developing nanomaterials and catalysts
for fuel cells since 1996. She worked for Japan Fine Ceramic Center,
Japan, Engi-Mat, Atlanta, and the National Research Council Canada,
Vancouver, before joining the University of Connecticut, Storrs, in 2010.
She has published more than 200 papers and is an inventor on eight
patents. She is a world-renowned expert in nanomaterials processing
for energy applications. A major component of her research has been
the development of new manufacturing processes for Solid Oxide
Fuel Cell (SOFC) and Proton Exchange Membrane Fuel Cell (PEMFC)
components that can potentially lower the cost of materials and
processing when compared to traditional fabrication techniques.
e:
radenka.maric@uconn.eduRadenka Maric
University of Connecticut, USA
Novelties in additive manufacturing and bio-printing
Notes: